More Flexibility for order picking, personnel and products
Customer case: Electrolux Distriparts AB
Electrolux Distriparts AB with 200 employees, is situated just outside Jönköping at the southern end of the lake Vättern. It is one of Sweden’s most important areas in terms of logistics. The company is responsible for the distribution of spare parts and accessories for the Electrolux Group and Husqvarna AB. Companies with well-known brands and products within gardening and appliances. For example AEG-Electrolux, Zanussi and Frigidaire. More than 40 million items for professionals and household work are sold every year to 150 different countries by Electrolux. That makes them world-leaders.
In 2007, the company carried out a large warehouse project, replacing a crane installation from the seventies, with manual order picking. During the period up until January 2008, 35 km with shelves were switched and more than 80,000 different articles were placed in new shelves. The decision was based on difficulties to get spare parts for the older warehouse, and also the strive for higher flexibility.
Flexibility was one of the key factors when analyses were carried out and finished concerning personnel, warehouse capacity and picking speed. When they started to use the new warehouse system, 9 trucks from Helge Nyberg AB were delivered. Today they have 15 of the same truck model with step trolleys for order picking at the warehouse.
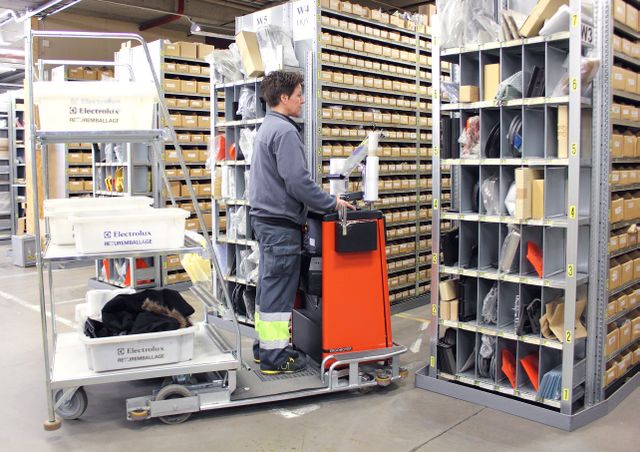
Guide rails in the floor simplifies the truck operator’s work when picking. The 2,8 meter picking height is easily reached using the steps.
" – The trucks are very ergonomic with the very low instep. We can also drive them on the mezzanine floors. With this solution, order picking never hits stops."
Stipe Milicevic, Process Developer Elextrolux Distriparts
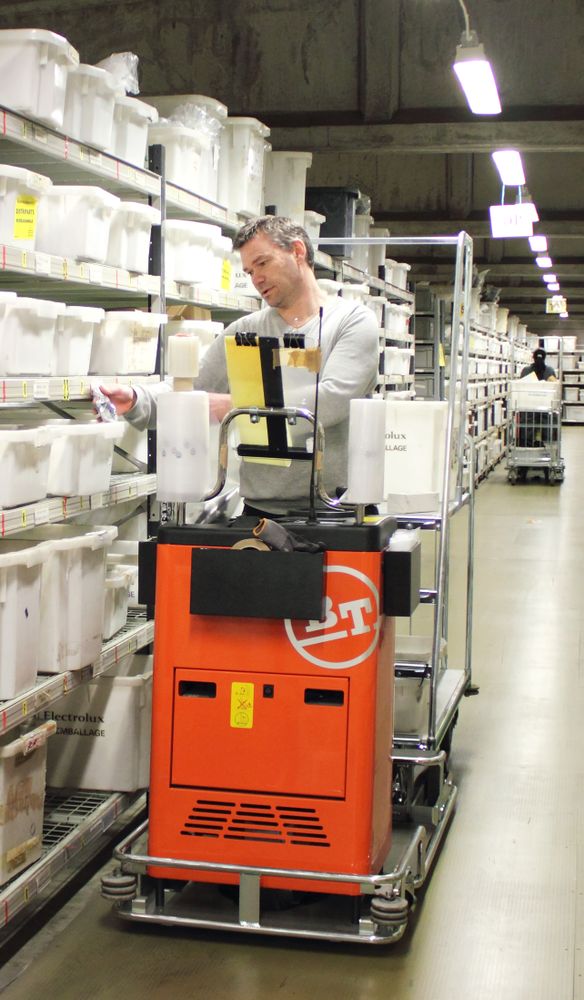
Approximately 14,000 order lines are picked each day, corresponding to 150,000 pieces. The articles are distributed in different warehouse sections, placed in boxes and sorted by picking frequency. Where these trucks are used, the maximum picking height is 2,8 m. One section is placed on a mezzanine floor with ramp access. Peak season is in May/June. If necessary then, manual trolleys from Helge Nyberg AB are used for order picking as well.
Intelligent Solutions
The traffic in the picking areas runs smoothly, since the boxes are distributed following a logic pattern based on picking frequency.
Stipe Milicevic, Process Developer at Electrolux Distriparts stresses the importance of flexibility. And trusting the use of common sense.
”With flexible solutions one avoids the vulnerablility which can occur if a crane installation stops. With a truck and trolley solution, plus manual trolleys, order picking never hits stops. ”In that way we avoid delays and effectively compensate for seasonal varations”, says Stipe.
”The trucks are very ergonomic with the very low instep. We can also drive them on the mezzanine floors. The trolleys, with steps adjusted to our picking heights, were constructed by Helge Nyberg AB according to our own requirements. The same applies to the hundered so or more manual trolleys they have delivered to us”, he concludes.
Valuable Knowledge and Experience
More material handling projects will occur in the future.
To have the experience and the knowledge from the project with the crane installation to manual picking, is assessed by Stipe Milicevic as a significant advantage. It will help in solving in-house logistics in a smart and effective way at the next stage of development.