Increased efficiency with trolleys instead of racking
Customer case: Blåkläder
The Value Added Service department at Blåkläder, Sweden, needed to get more space and streamline its production. Together with Helge Nyberg AB, an Ergobjörn trolley was designed that is fully adapted to Blåkläder’s needs.
They wanted to get rid of the fixed shelf rack for intermediate storage and instead replace it with trolleys. This not only saves space, but also time and the staff’s bodies.
Jeanette Nilsson is VAS Manager at Blåkläder, where VAS stands for Value Added Service. This is where the clothes get logos and names printed or embroidered.
One of her assignments is to increase capacity and improve the efficiency of the department, and through a collaboration with Helge Nyberg AB, many benefits have been gained.
– Helge Nyberg is good at adapting what you need. I like that you are not referred to a specific solution, but you get what works best just for us, says Jeanette Nilsson.
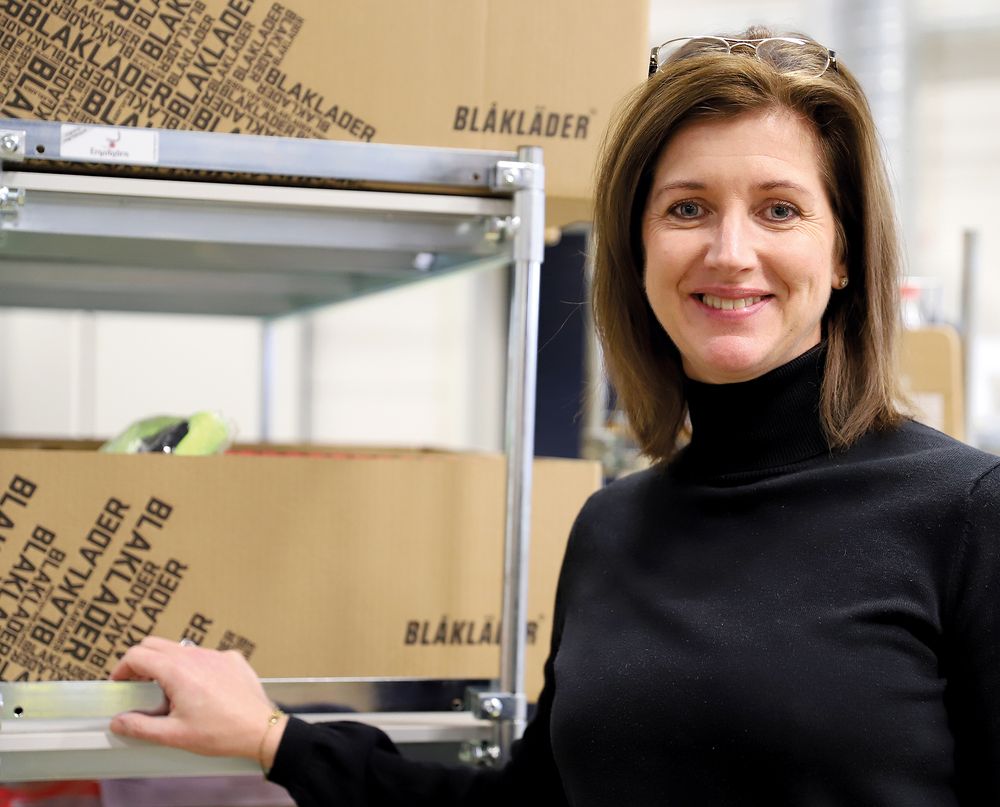
" – We have saved both time and bodies on these new trolleys."
Jeanette Nilsson, VAS-manager Blåkläder
Ungainly racks and much lifting
The purpose of the change was that Blåkläder needed to increase the number of printing machines. In the past, there was the fixed shelf rack that took up a lot of floor space and had shelves that was partly empty.
– We had several intermediate storages when boxes were moved from line to shelf, from shelf to trolley, from trolley to shelf, from shelf to workstation. There were much lifting and took a lot of time, Jeanette Nilsson says.
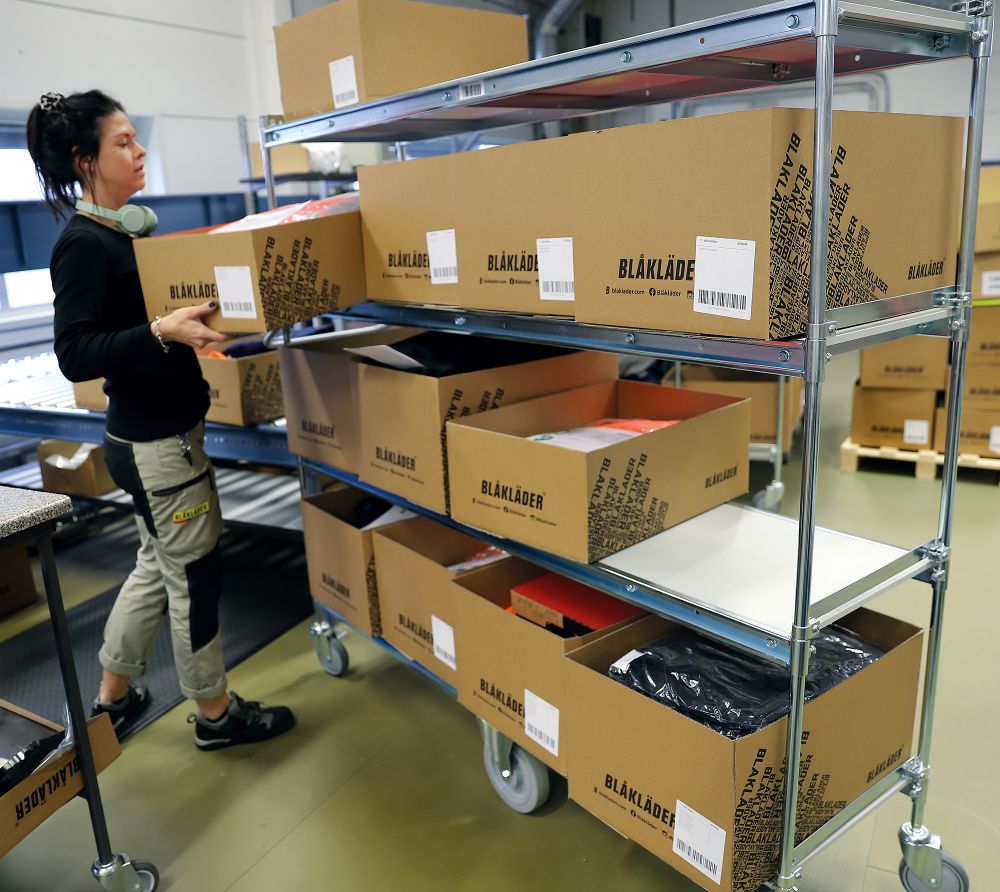
Smooth flow in the premises
On the other side of the wall is a large robotic warehouse that fills boxes with articles. One box for each order, which then enters the VAS department on a assembly line.
There are four departments to which the boxes are sorted. Embroidery, transfer, sewing and special packing. Orders are divided into the categories small, medium and large, which refers to volume.
Medium orders are the largest order category. These orders are put directly on an Ergobjörn trolley, which stands next to the assembly line.
Each trolley is a mobile storage space that is provided with a barcode. All boxes that are loaded on the trolley are scanned onto the trolley barcode.
– This means that we can easily track the order, says Jeanette Nilsson.
Customized trolleys
The Ergobjörn trolleys have been specially adapted for Blåkläder with a rail at the short end and shelves completely without edges, so that the box can slip on easily. The width of the trolley is also adapted to the size of the boxes.
– The trolleys are incredibly easy to drive, says Jeanette. They have saved us both time and bodies.
When a trolley is fully loaded, it runs a few meters to the transfer shelves. Here are the customers’ logos and badges to be printed on the clothes. The transfers are put directly into the correct box and then the trolley is parked waiting for the operator.
One of the largest in Sweden
Blåkläder is one of Sweden’s largest manufacturers in the heavy-duty working garment field. They develop, produce and distribute workwear, gloves and shoes for tradesmen and the annual production is about 3 million garments. Blåkläder acts in an international market and has been around since 1959.
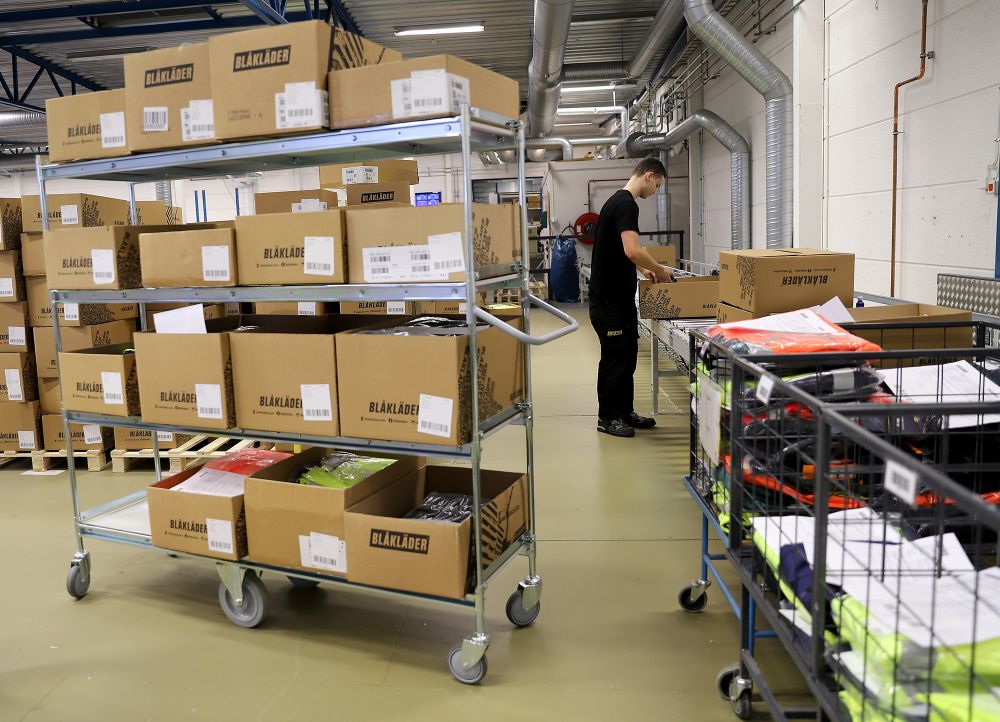