Electric trolleys efficiency the picking
Customer case: Yves Rocher
At Yves Rocher in Helsingborg, Sweden, they’re sending up to 15.000 packages a day. To pick straight into the delivery boxes has efficiency the flow and with the new trolleys with electric engines they have been able to increase the capacity. The result is very satisfied personnel who picks more efficiency and at the same time more ergonomic.
Yves Rocher is the number one cosmetic brand in France. In Sweden, Yves Rocher is a traditional e-commerce business with the central warehouse in Helsingborg. This is were they pick and send goods to customers throughout the Nordic region.
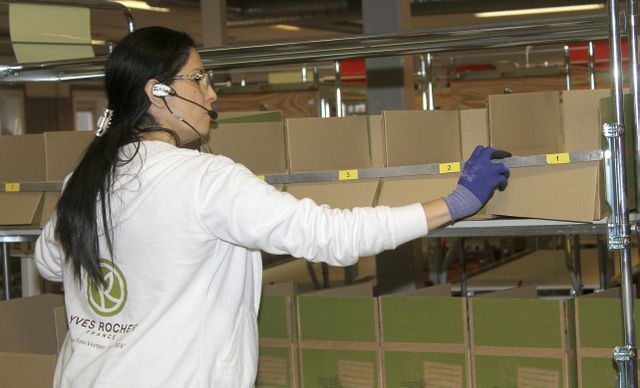
A special bar keeps the carton flaps in place.
Many years of cooperation
Helge Nyberg AB delivered the first trolley to Yves Rocher in the 80’s and over the years several trolleys has been delivered and tested in the production.
Mats Brafors, the distribution manager, says that they previously picked in boxes and then lifted the goods to a packing table and after that packed into the delivery boxes.
To eliminate unnecessary elements and become more flexible, they determined that they wanted to develop the trolley and be able to pick as many orders as possible at a round.
With the new trolleys, they place 42 orders and they’ve got rid of the intermediate station. Yves Rocher picks directly into the delivery boxes and the sizes of the boxes varies. The system sorts the orders so that the box size fills a trolley, and leaves as little empty space as possible.
When the trolley is full, the boxes are lifted over to a conveyor, where they automatically get address labels, will be weighed, sealed and sorted.
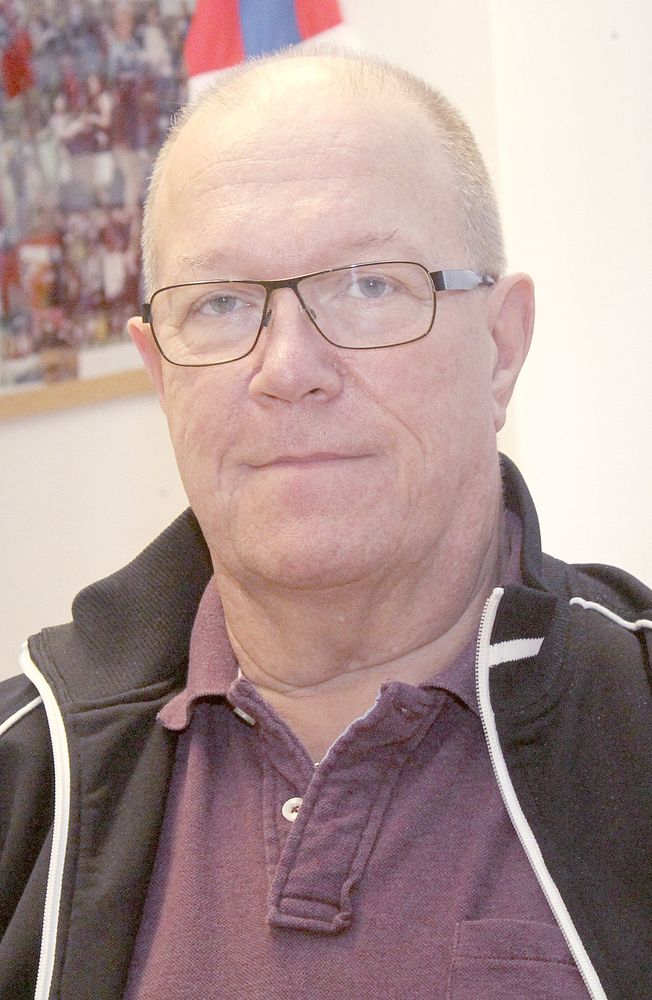
" – The cooperation with Helge Nyberg AB works very well. They understand exactly what we need."
Mats Brafors, distribution manager Yves Rocher
Electric trolleys
When the number of orders on a trolley increased, it also became heavier to pull with a full load. The stress for the body gets easier with the choice of motorised trolleys. With a touch on one of the handles, the trolley is driven forward or backwards.
When the personnel tried the new trolleys, they wanted to pull the trolley behind them at the same speed as when they push it in front of themselves. Since it’s possible to program the speed of the trolleys, this wasn’t any problems. Now the trolleys is as fast in both directions, which is very appreciated by the personnel.
The ergonomics of the picking has improved and it’s experienced as very positive for the company.
No unnecessary steps
– The cooperation with Helge Nyberg AB works very well. They understand exactly what we need, says Mats Brafors.
With the new trolleys they’re packing about two trolleys per hour per person. That means approximately 1.050 picks or 100 boxes an hour. Thanks to the continuously work with compressing the picking and the thought of planning the route with no unnecessary steps, the picking frequency is high.
The average packages sent in a day is 8.000 and the peaks may be up to 15.000 a day.
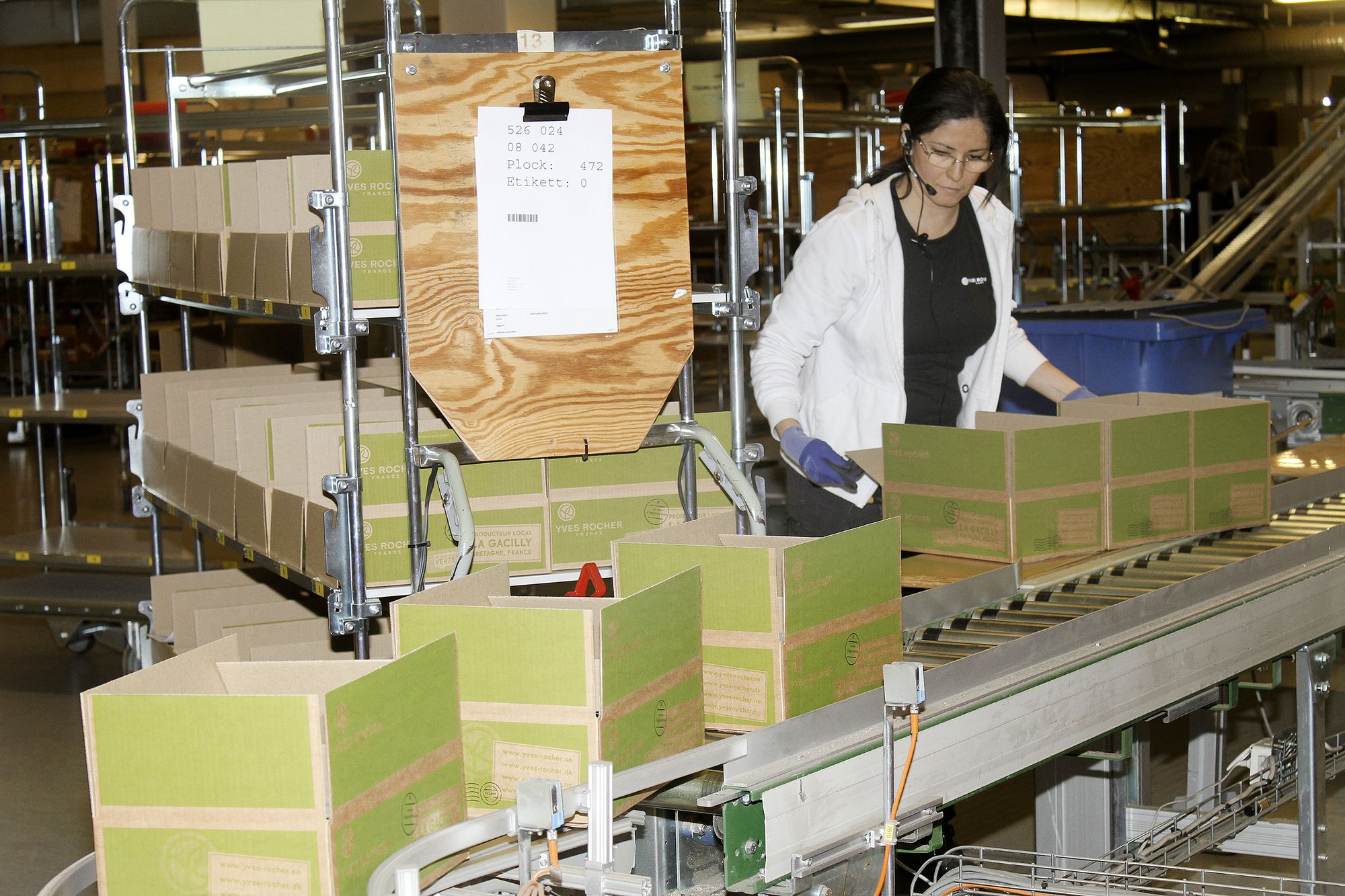
At Yves Rocher they use pick-by-voice, wich has reduced the errors.
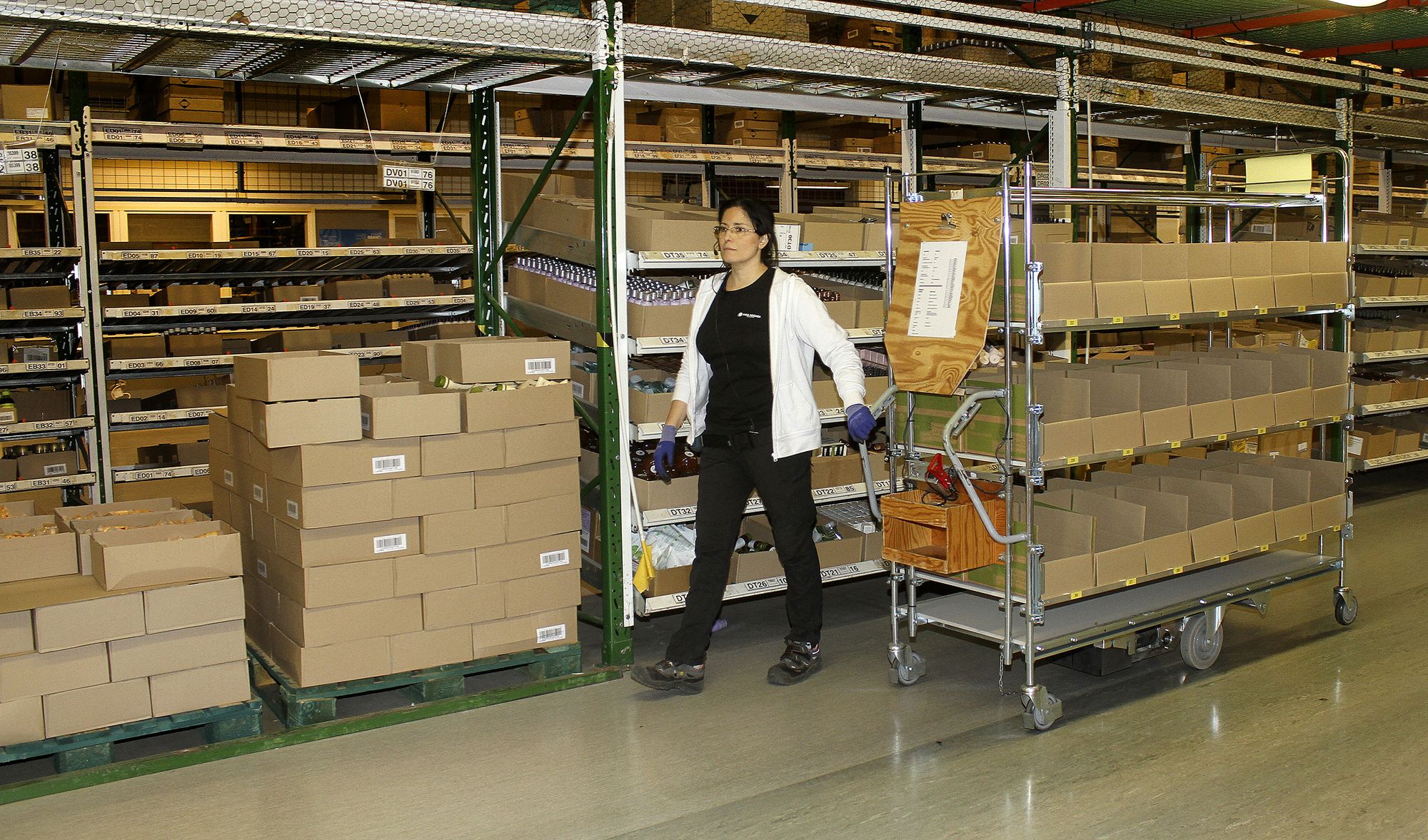