Trucks and trolleys for material handling efficiency
Customer case: Electrolux Laundry Systems
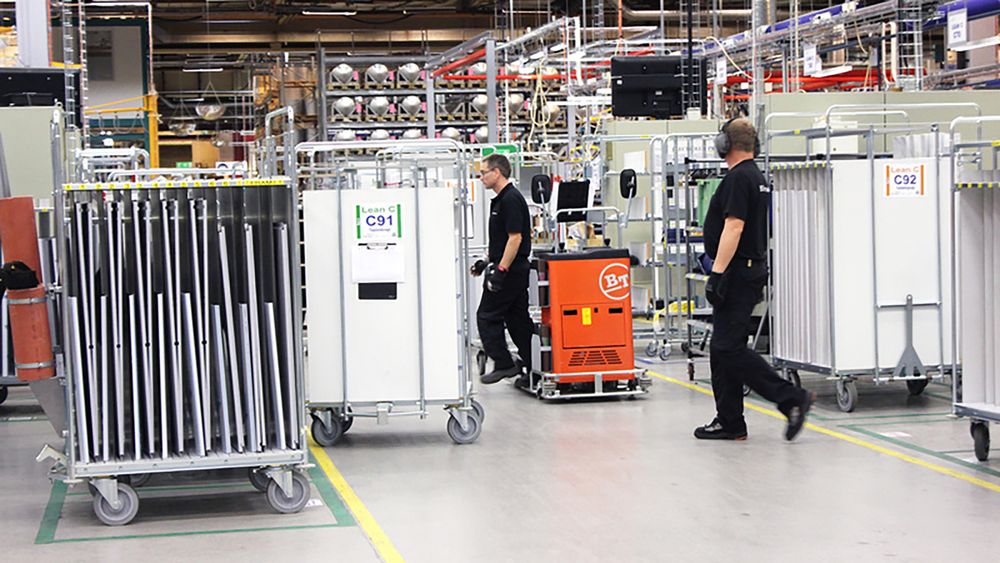
Electrolux Laundry Systems customises laundry equipment for professional use in hotels, apartment buildings, hospitals etc The Head office is in Ljungby in Småland.
Approximately 1,100 employees work on the production line in Sweden, France and Thailand. The goods are distributed through 19 sales offices worldwide.
Customers are placing greater demands on a short lead time. The production manager Richard Karlsson, previously a production technician at Electrolux, was given the task of organizing the routines in the Swedish factory. He has tested different methods through trial and error and created a new structure for material handling efficiency.
At an early stage he contacted Helge Nyberg and together with its design engineers they have developed a successful concept.
" – With the help of trains from Helge Nyberg AB materials arrive on time and in the correct place."
Rikard Karlsson, production manager Electrolux Laundry Systems
Streamline a More Efficient Work Flow
– In 2005, the management team made the decision to work according to the philosophy of Lean Production, says Rikard Karlsson. In 2007 we started a pilot project to have more control over the production line and to work with a clear structure in order to lower the turnaround time from order to customer and to have access to a greater assortment of materials.
– At the same time Helge Nyberg joined the co-operation and designed the first component of the component truck and trolley system, consisting of nine carriages drawn by an electric forklift truck. Instead of, as previously, having all the material in different pallet racks, which at times were difficult to find, the material began to be picked in the sequences of the carriages to be driven further by the trucks to the assembly point.
– The only thing that the assembly department now had to worry about was that the right truck and trolley came with the right material at the right time, just in time. A great deal of time was saved and this resulted directly in the fitters having a more comfortable pace of work and they could focus on the assembly.
Towing systems
– As the first production line was a success, I was asked how I wanted to proceed. I began to outline the next production line based on the requirements, location and quality objectives. It was now that the major physical change took place.
– Each year, we have adapted a new production line to Lean and currently we have four lines and a fifth in the pipeline for the same concept. From a pushing system, we have gone over to a system which pulls the material in trolleys by trains to the assembly point. Pull instead of push. An attractive system that minimizes overproduction and saves time
– Quality has increased significantly, as well as productivity and delivery reliability. With the help of trains from Helge Nyberg, material arrives on time and to the right place, says Rikard Karlsson. The size of the material has required a lot of special solutions. This adaptation and further development has taken place as a result of good cooperation.
Beneficial working methods
– The trolleys are divided into different compartments, making it easier for the fitters to get the material delivered at a good working height. Our cooperation in this project has been very enjoyable and stimulating for both parties, says Dan Karlsson, a salesman at Helge Nyberg.
They now have a total of 80 trolleys and five towing trucks from us. Work is to continue on line five that is in the planning stage executives and other companies will visit Electrolux in Ljungby to learn about the successful development of the Ljungby plant.